Nurturing a Continuous Improvement Culture
Share now
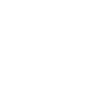
A continuous improvement culture within an organization is a relentless pursuit of advancement achieving operational excellence across all areas of operation. It can be presented as an iterative process of identifying, implementing, and evaluating changes rather than hoping for one big dramatic push to ignite growth . This progressive approach cultivates innovation, efficiency, and a profound sense of accountability and a growth mindset among employees. For changes and improvements that last, continuous improvement is the way to go. Because if you stop and think about it, you never really stop learning.
An organization that has a continuous improvement culture plays is always pushing for its team to be better, gaining more knowledge, and always improving, enhancing its overall competitiveness. Such an organization, business, or agency will ensure they stay ahead of the pack. Continuous improvement also supports the practice of listening to feedback, whether from shareholders or customers. And will be observed through the ongoing refinement of processes and products while driving workflow optimization and eliminating waste. No more time zombies!
In this article, 8 Figure Agency wants to show you how you too can nurture a continuous improvement culture in a few simple steps. We will show you that by perpetually refining products, services, and experiences, you can surpass customer expectations, satisfaction, and loyalty. To learn more about the process in depth:
Historical Context
The concept of continuous improvement has deep historical roots, drawing from pivotal movements such as Scientific Management which began its development in the 1880s and 1890’s. Pioneered by Frederick Winslow Taylor, it focused on efficiency through meticulous time and motion analysis. Post-World War II Japan introduced Kaizen which is a compound of two Japanese words that translates to “Good Change”. Kaizen emphasizes gradual, ongoing improvement, notably integrated into the Toyota Production System (TPS).
Following those developments we have Total Quality Management (TQM) which was popularized by W. Edwards Deming in the mid-20th century. It highlighted customer-centricity, continuous enhancement, operational excellence, and employee engagement in quality control. He came to be known as the father of quality control, quality circles, and the quality movement as a whole.
These historical frameworks underpin modern continuous improvement methodologies like Lean Manufacturing and Six Sigma, demonstrating the enduring influence of these foundational principles on contemporary organizational practices.
Fundamentals of Continuous Improvement
Now that we have a better understanding of what the continuous improvement mindset is and where it originated it’s time to break down the foundation of core principles and key components that make up continuous improvement.
Core Principles
The core principles that we touched on initially are:
Kaizen Philosophy
Kaizen , a Japanese philosophy of “good change,” advocates for small, continuous improvements in business. These small, incremental improvements promote perpetual progress through inclusive participation, respect for each individual’s contributions, and leveraging small adjustments for significant outcomes. This philosophy encourages increased efficiency, quality, innovation, and morale.
In lean manufacturing, Kaizen is foundational and is often seen in practices like identifying bottlenecks, standardizing procedures, and rapid improvement initiatives.
Lean Thinking
Lean thinking is centered on maximizing customer value by minimizing resource usage, eliminating waste, and optimizing processes. At its core, it revolves around delivering customer-defined value , eliminating seven types of waste, ensuring smooth workflow, and transitioning from push-to-pull systems based on demands.
Embracing continuous improvement opportunities through lean thinking puts the focus on employee involvement, experimentation, and adaptability.
Key Components
The key components of a continuous improvement culture as we’ve seen are:
Employee Involvement
Empowering employees is the basis on which the continuous improvement process is built. When employees closest to the work can identify inefficiencies and suggest solutions, it leads to more effective improvements. This fosters a sense of ownership and increases buy-in for new processes.
Data-Driven Decision Making
Effective improvement relies on data and not hunches to build a solid foundation . Collecting and analyzing data about processes, products, and customer feedback allows for a fact-based approach to identify areas for improvement and measure the impact of the necessary changes. This ensures that decisions are made based on evidence, not assumptions.
Building Blocks of a CI Culture
A thriving continuous improvement culture doesn’t happen by accident. It requires a deliberate effort to establish the right building blocks.
Leadership Commitment
It starts with leadership. Leadership sets the tone for the entire organization to improve continuously. A strong commitment to continuous improvement from leadership can present in different ways including:
Top-Down Support
Leaders need to not only endorse the concept but actively engage in actions that reinforce its importance throughout the organization. This includes allocating adequate resources, whether financial or human, to support improvement initiatives. Leaders must ensure that there is a dedicated budget for continuous improvement efforts, signaling its significance within the organization’s priorities. Their visible involvement not only sets an example for others but also communicates their commitment to the process. This sets the stage for leading by example.
Leading by Example
Leading by example in continuous improvement is more than just endorsing the idea. It requires leaders to embody the principles they advocate . This means actively participating in improvement initiatives alongside their teams, demonstrating a hands-on approach to problem-solving, and engaging in the same learning and adaptation processes they encourage among employees. Specifically, lean leadership leaders should exhibit a genuine enthusiasm for learning and self-improvement.
By doing so, leaders not only demonstrate humility and vulnerability but also create a culture where continuous learning is valued and encouraged at all levels of the organization.
Employee Empowerment
Employees are the backbone of any continuous improvement effort. Empowering them fosters a sense of ownership and fuels the strong continuous improvement culture that you want for your business.
Training Programs
Training programs aimed at fostering a culture of continuous improvement should be comprehensive and tailored to the specific needs of employees and the organization as a whole. It should involve teaching problem-solving tools, continuous improvement tools, data analysis techniques, and lean principles to develop broader competencies that support continuous improvement initiatives.
For instance, communication and collaboration skills are essential for effectively working in cross-functional improvement teams. However, some emphasize the importance of critical thinking and creativity in problem-solving.
Encouraging Innovation
Encouraging innovation requires creating an environment where employees feel comfortable suggesting ideas and experimenting with new approaches. No more traditional suggestion boxes or feedback channels, try implementing organic strategies to create an environment conducive to innovation. This can be achieved by dedicating time and resources to innovation activities such as regular hackathons, innovation challenges, or brainstorming sessions where employees are allowed to explore new ideas and collaborate with colleagues from different departments or backgrounds.
Implementing Continuous Improvement
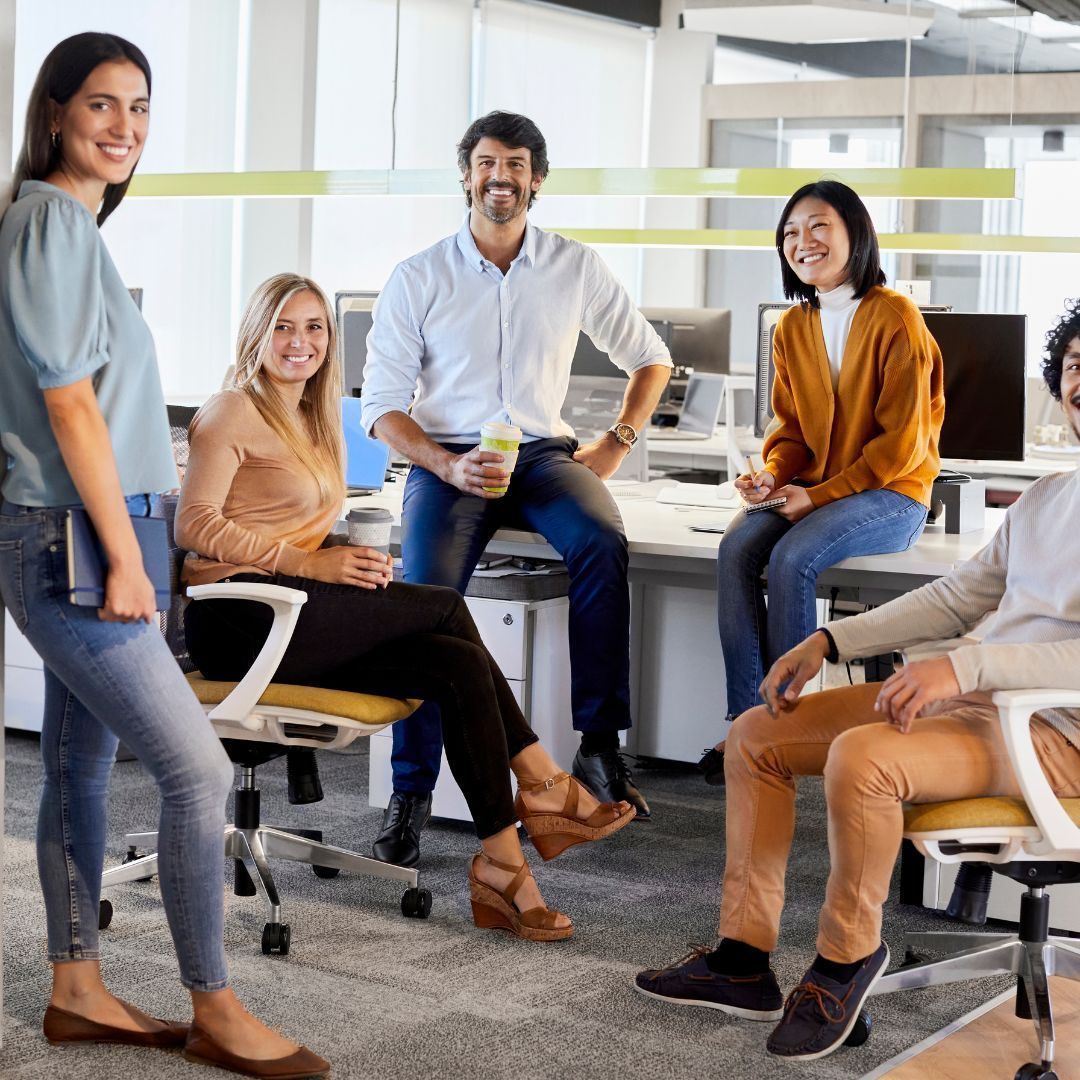
If you want to reap the benefits of the continuous improvement approach, it’s time to put theory into practice.
Process Mapping
As a fundamental tool for the continuous improvement of organizational culture, process mapping visually depicts the steps involved in a process, from start to finish.
Identifying Bottlenecks
Process mapping helps identify bottlenecks – any step in the process that slows down or hinders overall efficiency. By visualizing the workflow, you can pinpoint areas where tasks are duplicated, unnecessary delays occur, or resources are underutilized . These can take the form of flowcharts, swimlane diagrams, or value stream maps which then allow stakeholders to gain a clear understanding of the entire process flow, including inputs, outputs, decision points, and handoffs between different stages.
Value Stream Analysis
This technique takes process mapping a step further. It analyzes each step in the process to determine if it adds value for the customer. Value-added activities are those that directly contribute to transforming inputs into outputs that meet customer needs. Non-value-added activities (waste) consume resources but don’t add value. In other words, Time Zombies. This is how value stream analysis helps identify opportunities to eliminate waste and streamline the process.
Process mapping is heavily integrated into our 90-Day Road Map for the businesses that partner with 8 Figure Agency. Let’s help you get your continuous improvement culture on track.
Technology Integration
In the 21st century and beyond, technology plays a crucial role in enabling and accelerating efforts towards a continuous improvement culture.
Automation Tools
Automating repetitive tasks can free up employee time and resources for more value-added activities. Enter process automation tools . This could come in the form of workflow automation software, data entry automation tools, or robotic process automation (RPA) depending on the specific tasks. These automation tools often include analytics and reporting capabilities that provide insights into process performance, identify bottlenecks, and measure the impact of automation initiatives.
Data Analytics
Data is the cornerstone of data-driven decision-making in a continuous improvement culture. Leveraging data analytics tools allows you to:
- Track performance: Monitor key metrics to identify areas for improvement and measure the impact of changes.
- Identify trends: Analyze data to uncover patterns and trends that may indicate potential problems or opportunities for improvement.
- Gain insights: Use data visualization tools to gain deeper insights into processes and customer behavior, informing better decision-making.
Overcoming Challenges
Even with a well-designed plan, implementing a continuous improvement culture can face hurdles. Here’s how to address two common challenges:
Resistance to Change
People naturally resist change, as they fear disruption and potential job insecurity.
Change Management Strategies
For effective organizational change, start by developing a comprehensive change management plan that guides the transition process. Pair that with clear and transparent communication regarding the reasons behind the change, the benefits for both employees and the organization, and a detailed timeline for implementation. This ultimately helps build trust and mitigate anxiety
You can then follow this by providing adequate training and support to employees enabling them to adapt to new processes and technologies in the evolving work environment.
Communication Plans
Develop clear and consistent communication plans to keep employees informed and engaged throughout the continuous improvement journey. To retain great employees , your team needs to be encouraged to regularly share updates on progress, success stories, and how improvements are impacting the organization. This can come in the form of:
- Stakeholder Analysis: Identify key stakeholders and tailor communication to their needs.
- Clear Objectives: Define goals for communication efforts.
- Multichannel Approach: Use various channels to reach employees.
- Consistent Messaging: Ensure coherence across channels.
- Two-Way Communication: Encourage feedback and participation.
- Regular Updates: Keep employees informed of progress.
- Training and Education: Provide resources and workshops.
- Recognition and Rewards: Celebrate employee contributions.
Sustaining Momentum
Maintaining the momentum of a continuous improvement culture contributes to the efforts going into long-term success. This can be accomplished by recognizing and rewarding great efforts as well as always providing the opportunity for ongoing training and development. Recognizing and rewarding employees who actively participate in continuous improvement efforts reinforces the desired behavior and motivates others to get involved. This can include public recognition, awards, or even performance-based incentives.
Measuring Success
Demonstrating the value of efforts toward a continuous improvement of corporate culture also requires a clear understanding of how to measure success.
Key Performance Indicators (KPIs)
KPIs are quantifiable measures that track progress towards achieving specific goals. KPIs for continuous improvements , help you assess the effectiveness of improvement initiatives and the overall health of your continuous improvement culture.
Metrics for Improvement
To effectively measure progress toward continuous improvement goals, it’s essential to identify relevant Key Performance Indicators (KPIs) that align with the objectives. These metrics should be related to:
- Efficiency: Lead time, cycle time, rework rates, throughput
- Quality: Defect rates, customer satisfaction scores, return on investment (ROI)
- Innovation: Number of new ideas submitted, time to market for new products
- Employee Engagement: Employee participation in continuous improvement initiatives, suggestions, and feedback loops.
Monitoring Progress
A baseline first needs to be established to measure the quality of changes that have occurred. These changes then need to be tracked regularly. Regular tracking and analysis of these metrics will gauge the impact of your continuous improvement efforts and the capacity to do more . This involves identifying trends and areas for further improvement based on the data collected.
Qualitative measures such as employee surveys and feedback sessions can offer valuable insights into aspects like engagement and morale. Employing a balanced scorecard approach allows for a more comprehensive evaluation of the success of the continuous improvement culture. Benchmarking against industry best practices or competitors can also serve to provide valuable comparative insights to identify areas for enhancement and maintain competitiveness and competitive advantage.
Summary
By embracing a continuous improvement culture, organizations can unlock a continuous cycle of improvement which will propel them towards long-term success, a healthy culture, and sustainable growth. Research shows that forming a new habit can take 5-254 days. Let’s show you what other improvement ideas we can help your business or agency achieve in just 90 days.
The post Nurturing a Continuous Improvement Culture appeared first on 8 Figure Agency.
Search
Recent Post
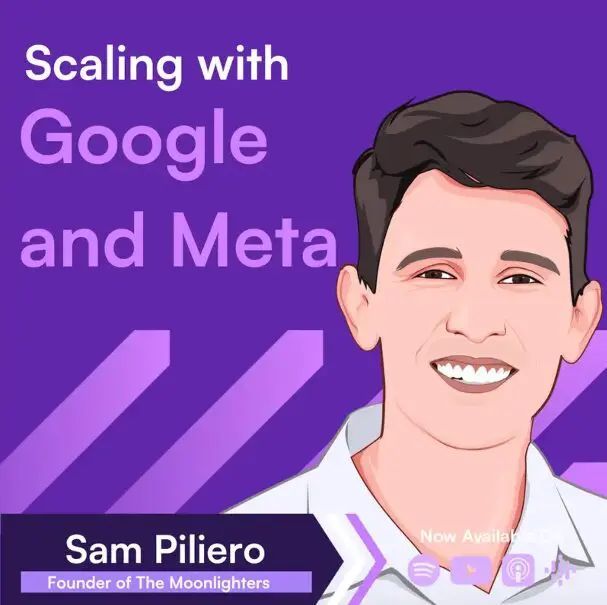